Model Item | GC30-NG | GC40-NG | GC50-NG | GC80-NG | GC120-NG | GC200-NG | GC300-NG | GC500-NG | ||
Rate Power | kVA | 37.5 | 50 | 63 | 100 | 150 | 250 | 375 | 625 | |
kW | 30 | 40 | 50 | 80 | 100 | 200 | 300 | 500 | ||
Fuel | Natural Gas | |||||||||
Consumption(m³/h) | 10.77 | 13.4 | 16.76 | 25.14 | 37.71 | 60.94 | 86.19 | 143.66 | ||
Rate Voltage(V) | 380V-415V | |||||||||
Voltage Stabilized Regulation | ≤±1.5% | |||||||||
Voltage Recovery Time(s) | ≤1.0 | |||||||||
Frequency(Hz) | 50Hz/60Hz | |||||||||
Frequency Fluctuation Ratio | ≤1% | |||||||||
Rated Speed(Min) | 1500 | |||||||||
Idling Speed(r/Min) | 700 | |||||||||
Insulation Level | H | |||||||||
Rated Currency(A) | 54.1 | 72.1 | 90.2 | 144.3 | 216.5 | 360.8 | 541.3 | 902.1 | ||
Noise(db) | ≤95 | ≤95 | ≤95 | ≤95 | ≤95 | ≤100 | ≤100 | ≤100 | ||
Engine Model | CN4B | CN4BT | CN6B | CN6BT | CN6CT | CN14T | CN19T | CN38T | ||
Aspration | Natural | Turboch arged | Natural | Turboch arged | Turboch arged | Turboch arged | Turboch arged | Turboch arged | ||
Arrangement | Inline | Inline | Inline | Inline | Inline | Inline | Inline | V type | ||
Engine Type | 4 stroke, electronic-control spark plug ignition, water cooling, | |||||||||
premix proper ratio of air and gas before combustion | ||||||||||
Cooling Type | Radiator fan cooling for closed-type cooling mode, | |||||||||
or heat exchanger water cooling for cogeneration unit | ||||||||||
Cylinders | 4 | 4 | 6 | 6 | 6 | 6 | 6 | 12 | ||
Bore | 102x120 | 102x120 | 102x120 | 102x120 | 114x135 | 140x152 | 159x159 | 159x159 | ||
X Stroke(mm) | ||||||||||
Displacement(L) | 3.92 | 3.92 | 5.88 | 5.88 | 8.3 | 14 | 18.9 | 37.8 | ||
Compression Ratio | 11.5:1 | 10.5:1 | 11.5:1 | 10.5:1 | 10.5:1 | 0.459027778 | 0.459027778 | 0.459027778 | ||
Engine Rate Power(kW) | 36 | 45 | 56 | 90 | 145 | 230 | 336 | 570 | ||
Oil Recommended | API service grade CD or higher SAE 15W-40 CF4 | |||||||||
Oil Consumption | ≤1.0 | ≤1.0 | ≤1.0 | ≤1.0 | ≤1.0 | ≤0.5 | ≤0.5 | ≤0.5 | ||
(g/kW.h) | ||||||||||
Exhaust Temperature | ≤680℃ | ≤680℃ | ≤680℃ | ≤680℃ | ≤600℃ | ≤600℃ | ≤600℃ | ≤550℃ | ||
Net Weight(kG) | 900 | 1000 | 1100 | 1150 | 2500 | 3380 | 3600 | 6080 | ||
Dimension(mm) | L | 1800 | 1850 | 2250 | 2450 | 2800 | 3470 | 3570 | 4400 | |
W | 720 | 750 | 820 | 1100 | 850 | 1230 | 1330 | 2010 | ||
H | 1480 | 1480 | 1500 | 1550 | 1450 | 2300 | 2400 | 2480 |
GTL GAS GENERATOR
The world is experiencing steady growth. The total global&demand for energy will grow by 41% up to 2035. For over 10 years, GTL has worked tirelessly to meet the growing&demand for energy, prioritising the use of engines and fuels&which will ensure a sustainable future. GAS generator sets which are powered by environmentally&friendly fuels, such as natural gas,biogas,coal seam gas esandassociated petroleum gas.Thanks to GTL’s vertical manufacturing process, our equipmenthas proven excellence in the use of the latest technology during manufacture and the use of materials that ensure quality performance which surpasses all expectations. Gas Engine Basics The image below shows the basics of a stationary gas engine and generator used for the production of power. It consists of four main components - the engine which is fueled by different gases. Once the gas is burnt in the cylinders of the engine, the force turns a crank shaft within the engine. The crank shaft turns an alternator which results in the generation of electricity. Heat from the combustion process is released from the cylinders;This must be either recovered and used in acombined heat and power configuration or dissipated via dump radiators located close to the engine. Finally and importantly there are advanced control systems to facilitate robust performance of the generator. 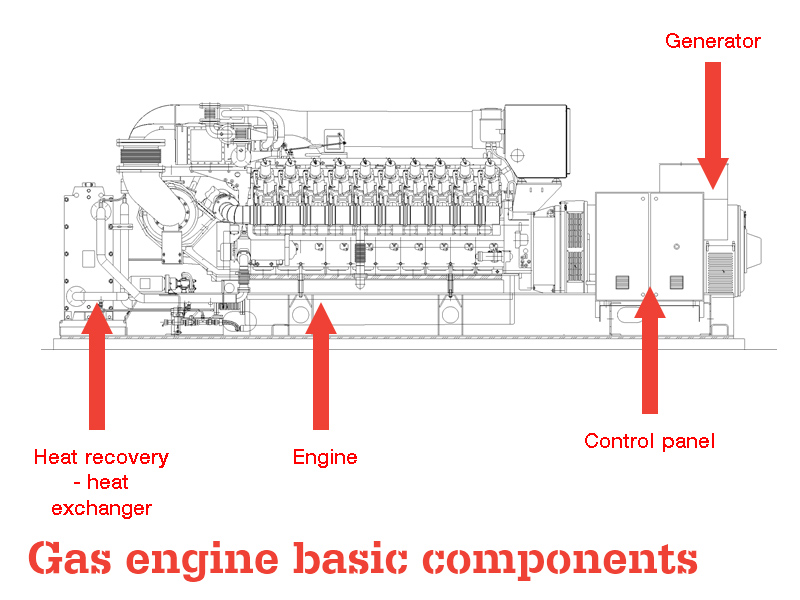
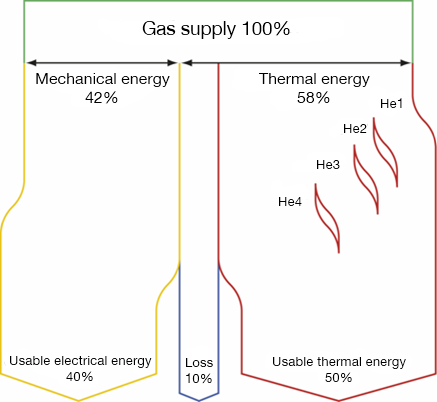